Pitch control and yawing: systems for optimal wind turbine design
- Windenergy
- 20.11.2022
- Reading Time: {{readingTime}} min
- Share Article
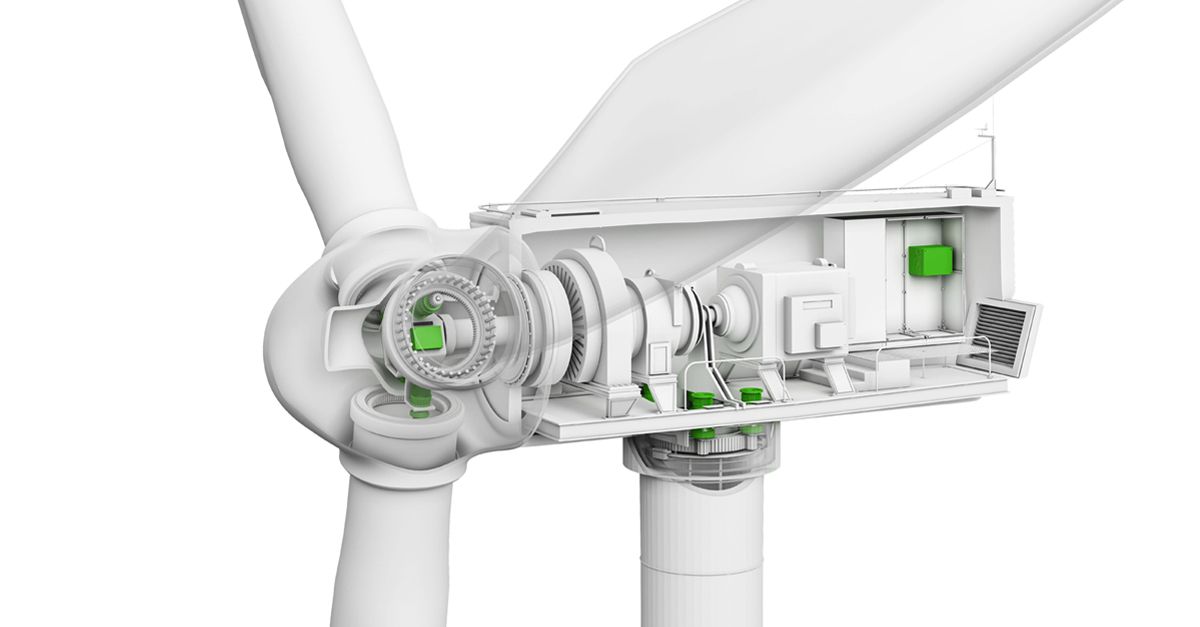
Contents
In order to install a highly complex wind turbine or even a complete wind farm consisting of multiple power generating units, there are many aspects to take into consideration apart from the wind conditions.
There is the local infrastructure, but also other factors such as grid connection options, adequate distance from residential areas, as well as certain safety precautions and legal framework conditions.
Satisfying the increasing demand for power in the future requires ever greater and more powerful wind energy systems, both onshore and offshore. Ensuring the power and performance of these generators calls for reliable and safe solutions. At the same time, renewable energies are under enormous economic pressure to keep the levelized cost of electricity as low as possible.
Against this background, today’s most commonly used design for wind turbines is the three-blade upwind turbine with horizontal axis and rotor. The pitch system regulates the power output of the wind turbine by adjusting the rotor blades; at the same time, it functions as the main brake. This is absolutely crucial for ensuring the greatest possible efficiency of the wind turbine and the highest possible energy yield. The implementation of this highly complex operation relies on multiple closed-loop control systems.
Currently, almost all wind turbines use pitch control systems and yaw systems. The yaw drives control the alignment of the nacelle with the wind; the pitch control system is constantly adjusting the angle of attack of the rotor blades—the pitch angle—in order to achieve the greatest possible energy yield.
Pitch control systems
The pitch control system has been the gold standard for years when it comes to cost-efficient, robust rotor blade adjustment in wind turbines. In addition, the engineering design of the pitch systems can increase the availability of the wind turbines.
Recent improvements of functional safety were able to significantly reduce the material input, creating a decisive cost advantage.
How does this cost advantage manifest itself?
- First, there is less wear of the equipment because the application of a profiled emergency/safety motion reduces oscillations of the machine tower.
- Second, the material input can already be reduced in the planning stage of new wind turbines: For example, the planning can employ thinner steel walls and thinner bolts right from the start.
In addition, plants with pitch control don’t need a mechanical main brake because the pitch system takes over this functionality through the adjustment of the rotor blades, achieving aerodynamic deceleration of the turbine rotation.
Another pitch system feature is the application of the angle of attack. This feature automatically adjusts the rotor blade position between zero and maximum lift. The pitch control system also maintains the optimal rotational speed for maximum energy conversion efficiency.
Pitch-controlled cut-in and cut-out wind speed
The wind turbine’s central control system constantly determines the wind speed in order to ensure that the plant is always running inside the optimal range.
This range is determined by several factors (e.g. rotor diameter, noise emissions, etc.): The tip speed (80-90 m/s) for example, represents a fundamental design factor for the aerodynamic properties of the wind turbine.
As soon as the wind speed drops below the threshold required for cost-effective operation (in very low winds, approx. below 2.5 m/s), the turbine goes into idle mode.
Conversely, in high winds (12–25 m/s) the power output of the plant must be limited. The pitch system sets the rotor blades to the required pitch angle, which regulates the lift of the rotor blade and keeps the nominal power output of the plant at a constant value.

If the wind speed increases too much (at approx. 25 m/s), the plant shuts down in order to prevent mechanical overload caused by rotor overspeed.
Benefits of the pitch control system at a glance:
- Functions as rotor brake
- Keeps rotor running at optimal speed
- Eliminates torque variability almost completely
- Low-noise operation
Pitch control and azimuth systems ensure the best possible performance of wind turbines.
Yaw systems
To ensure alignment with the wind, yaw systems with controlled multi-axis drive systems have become the standard for efficient wind energy. The ultra-modern method employed by these drives is the dynamic synchronization of multi-axis systems.
And with good reason: Compared to conventional concepts, a dynamically synchronized multi-axis drive yaw system provides numerous benefits. This includes a significantly higher energy yield thanks to the more precise alignment of the wind turbine.
In addition, it provides for optimal control of the acceleration and deceleration moments. Conventional solutions, by contrast, frequently involve abrupt start-up movements, which cause unwanted mechanical loads on the equipment and in turn more wear and tear.
This method also saves on the overall cost for the wind turbine: For example, it could eliminate the need for a hydraulic brake system at the yawing level.
However, the decision for a yaw system without a hydraulic brake is very complex. The system must fit into the overall plant design (safety for the servicing with other systems) and be included at the design stage already. Smart drive concepts with a broad performance range and active energy recovery, as well as robust, high-quality rotary encoders are other factors that can boost the benefits of the yaw drive even further. This also applies to the reliability and safety of the plant.
They are also an effective means to prevent expensive downtimes of the wind turbine. After all, the service life of a wind turbine is at least 25 years. This makes a low-wearing yaw control concept all the more necessary.
Conclusion: pitch and yaw systems—solutions for optimal wind turbine design
In the energy mix, wind turbines come with low levelized cost of electricity. This makes them an important and competitive solution compared to conventional power generation, in particular with a view to the challenges of the energy transition.
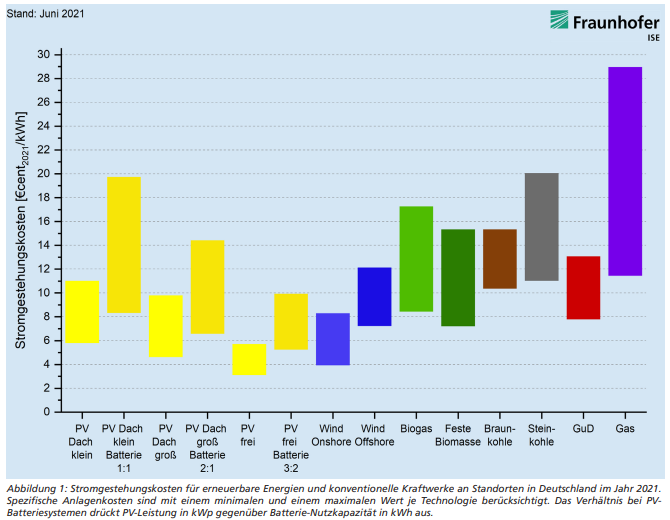
However, the levelized cost of electricity of wind turbines depends to a high degree on the conditions at the particular wind site.
In order to achieve optimal wind turbine performance, pitch control systems and yaw systems are today’s state of the art. They constantly adjust the orientation of the nacelle and rotor, as well as the pitch angle of the individual rotor blades, to ensure optimal alignment with the prevailing wind direction. This achieves a constant power feed into the grid at maximum yield.
These systems also help reduce the cost of the wind turbine significantly and guarantee many years of service life.